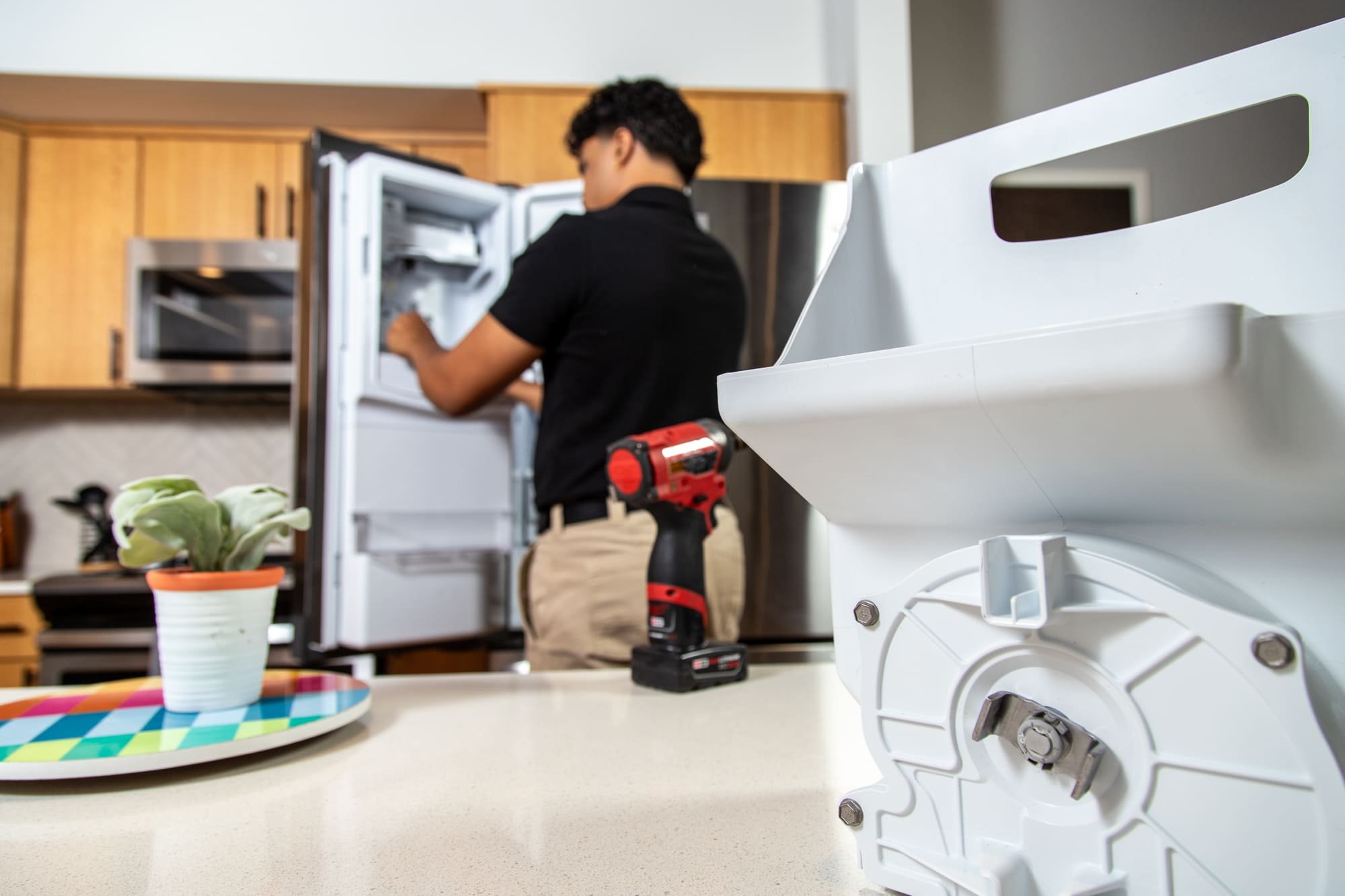
Ice Maker Repair in Farragut, TN
Working With A Purpose, True Service!
-
Working With A Purpose, True Service! -
Ice maker repair services in Farragut, TN, address a spectrum of common issues that can impact the functionality of this essential appliance. Problems such as a lack of ice production, slow ice-making, or irregular cube sizes can disrupt daily convenience. Professional technicians with the right tools and knowledge diagnose and repair these problems promptly, restoring the ice maker to optimal performance.
Reliable repair services focus on resolving mechanical or electrical malfunctions that develop over time. Regular use and occasional wear can lead to clogged water lines, defective motors, or sensor malfunctions. Addressing these issues with quality parts and thorough methods extends the appliance's lifespan, reducing the need for costly replacements. Restored performance also supports energy efficiency and consistent operation.
Local repair services in Farragut offer timely assistance for various ice maker models and brands. Professionalism and attention to detail throughout the repair process build trust and reliability. By resolving concerns effectively, these services help maintain a seamless household experience, allowing families and businesses to appreciate the comfort of a fully functioning ice maker. Dependable repair solutions contribute to the overall efficiency and ease of everyday life.
Common Ice Maker Issues We Repair in Farragut
-
Ice Maker Not Making Ice
When an ice maker stops producing ice, our experienced technicians investigate multiple potential causes. The issue often stems from clogged water lines, faulty water inlet valves, or problems with the thermostat. Our team brings specialized tools and parts to address these common problems efficiently. Regular maintenance helps prevent these issues from developing into more significant concerns.
-
Ice Maker Producing Low-Quality Ice
Cloudy, minor, or misshapen ice cubes indicate underlying problems that affect ice quality. Common culprits include mineral buildup in the water supply, incorrect temperature settings, or worn-out components. Our technicians thoroughly clean the system and calibrate all settings to restore proper ice production. Professional maintenance keeps ice makers operating at peak performance.
-
Ice Maker Freezing Up
Frost accumulation and complete system freezing typically result from problems with the defrost cycle or temperature control systems. Our skilled technicians identify the root cause, whether it's a malfunctioning defrost timer, broken thermistor, or issues with the control board. Swift intervention prevents damage to other components and restores regular operation.
-
Ice Maker Leaking Water
Water leaks can damage surrounding cabinets and floors while increasing utility costs. Familiar sources include cracked water lines, loose connections, or damaged seals. Our repair specialists locate the source of leaks and replace necessary components. Professional repairs prevent water damage and restore efficient operation.
-
Ice Maker Making Unusual Noises
Strange sounds during operation often signal mechanical problems that require immediate attention. These noises might stem from worn bearings, damaged fan motors, or loose components. Our technicians identify the source and replace worn parts before they cause additional damage to the system.
-
Ice Maker Not Ejecting Ice
The problem typically involves the ejector assembly or control mechanism when ice makers fail to release ice. Our technicians examine the ejector arms, motor, and associated components to identify mechanical or electrical failures. Professional repairs restore proper ice dispensing functionality.
Hear from our customers
Our Ice Maker Repair Process in Farragut
-
Initial Consultation
The repair begins by thoroughly discussing the ice maker's symptoms and history. Our technicians listen carefully to descriptions of the problems and ask relevant questions about recent changes in performance. This information helps narrow down potential causes and guides the diagnostic approach.
-
Diagnostic Assessment
Our technicians perform comprehensive system checks using advanced testing equipment to identify the exact cause of malfunction. This process includes examining electrical components, mechanical parts, and water supply systems. The thorough evaluation leads to accurate diagnosis and appropriate repair recommendations.
-
Repair Solutions
Based on diagnostic findings, our technicians implement targeted repairs using high-quality replacement parts and proven techniques. The work includes cleaning components, replacing worn parts, and adjusting settings. Each repair addresses both immediate problems and potential future issues.
-
Final Testing
Our technicians run the ice maker through multiple cycles to verify proper operation following repairs. This testing includes checking ice production quality, monitoring water flow, and confirming normal noise levels. The comprehensive testing process validates the effectiveness of repairs.
Maintenance Tips for Ice Maker in Farragut
-
Maintaining a clean ice maker prevents contamination and extends equipment life. Our technicians recommend sanitizing all ice-contact surfaces monthly with appropriate cleaning solutions. Regular cleaning removes mineral deposits, mold, and bacteria that can affect ice quality. Professional deep cleaning services target hard-to-reach components and eliminate stubborn buildup that impacts performance.
-
Water filter maintenance directly impacts ice quality and machine longevity. Regular filter inspections reveal signs of clogging or deterioration that affect water flow. Our specialists recommend monitoring water pressure and replacing filters according to manufacturer specifications. Professional filter maintenance prevents mineral buildup and improves ice clarity.
-
Water line problems often cause significant ice maker issues. Regular inspection reveals potential leaks, crimps, or blockages restricting water flow. Our technicians examine connection points and line conditions throughout the system. Professional maintenance includes pressure testing and line cleaning to maintain optimal water delivery.
-
Temperature control is crucial in ice production quality. The ideal temperature range varies by manufacturer and model specifications. Our technicians calibrate temperature settings and verify proper thermal cycling. Professional temperature management optimizes ice production while reducing energy consumption.
-
Proper drainage prevents water accumulation and potential damage. Regular drainage system inspection identifies blockages or slow-draining conditions. Our technicians clean drain lines and verify proper water flow throughout the system. Professional maintenance includes testing drain components and clearing any obstructions.
-
Strange sounds often indicate developing mechanical problems. Regular monitoring helps identify changes in operational sounds. Our technicians recognize various noise patterns associated with specific mechanical issues. Professional evaluation determines whether unusual sounds require immediate attention or routine maintenance.
Choose True Appliance Service for Ice Maker Repair in Farragut
-
Experienced Technicians
Our repair specialists bring extensive training and hands-on experience to every service call. Each technician undergoes continuous education on new ice maker technologies and repair techniques. This expertise translates into accurate diagnosis and effective repairs. Professional development keeps our team current with industry advances and manufacturer updates.
-
Customer Satisfaction Guarantee
Our commitment to excellence drives every aspect of our service delivery. We stand behind our work with comprehensive warranty coverage on parts and labor. Our team maintains open communication throughout the repair process. Professional service standards guide our approach to customer care.
-
Transparent Pricing
Our pricing structure eliminates surprises and hidden charges. Detailed estimates outline all necessary repairs and associated costs. Our technicians explain repair options and recommendations clearly. Professional service includes upfront pricing and precise documentation of all work performed.
-
Timely Service
Our efficient scheduling system minimizes wait times for repairs. Quick response times prevent minor issues from becoming major problems. Our technicians arrive prepared with standard replacement parts and specialized tools. Professional time management keeps projects on schedule and businesses operating smoothly.
True Appliance Service brings extensive experience and professional expertise to ice maker repairs in Farragut, TN.
The skilled technicians diagnose and fix issues promptly, using high-quality parts and proven repair techniques. With competitive pricing and reliable service, True Appliance Service stands ready to handle any ice maker repair needs. Contact our team for professional ice maker repairs that restore optimal performance and extend equipment life.